The SP has had more than 400 of it's bolts and washers replaced with aerospace items in the last 5 years. Proton uses metric sized fasteners on it's cars including the Putra. I am using aluminium and titanium fasteners in socket cap (allen) head, hexagon or flanged hexagon head styles. Common stainless steel is also sometimes used (when I can't afford Ti and aluminium is too weak). In general each material has it's strengths and weaknesses in which I'll try to cover. Hope I don't bore you to death.
Aluminium
I generally use aluminium fasteners on non-load bearing (non-stressed) areas. These are 7075T73 high tensile material and are either potassium bichromate coated (yellowish goldish tinge) or anodized (avail in red, blue, green, silver, black, purple and gold). Anodized aluminium fasteners are slightly more expensive than PB coated aluminium fasteners but do look better aesthetically (to most people). Beauty however is in the eye of the beholder as I prefer the PB coated AL fasteners. Also PB coated fasteners will not suffer from colour fading due to heat stress unlike anodizing. Aluminium has only 40% the mass of mild steel but unfortunately isn't as strong. You don't want those backyard special rougho macho mechs tightening these fasteners as they will strip them in no time. Picture below of aluminium fasteners with PB coating. Most Brit race teams including WRC, BTCC and GT teams use them a lot. Next time you look at racecars, try to spot them.

Picture below shows M6 X 20 sized socket cap head bolts and washers used on the SP's engine timing belt cover. M8 sized bolts are used to secure the power steering and air-conditioning lines.

Titanium
Titanium sounds cool, looks cool but unfortunately is most expensively NOT cool! The price is simply unimaginable. To give you a contrast the aluminium M6 bolt which I mentioned earlier might cost more than RM1 depending on the exchange rate. The titanium version will cost 10-15 times more. You'll have to shop around the Ti bolt suppliers as generally the price will vary quite a bit though it's the difference between stupendously expensive and very expensive. There are very few Ti fasteners on the SP and these are used for load bearing areas like the front and rear shock absorber top mounts and on the strut bars. The Ti material most widely used in motorsport fastener applications is Grade 5 titanium or 6AL-4V. This material has 60% the mass of mild steel which means that it's heavier than aluminium. The plus point is that titanium is very very strong, hard and stiff. Titanium is also very corrosion resistant and can be colour anodized (only in gold and blue though. Have not seen other colours). Care also has to be taken when tightening Ti fasteners as exceeding the quoted torque setting will cause galling. This is when the Ti bolt is sort of cold welded and no matter what you do you won't be able to loosen the fastener. And since Ti is super hard and strong, God Bless! Having said that I do not have any problems with galling (touch wood) though to eliminate this problem you might want to apply anti-seize or moly paste to the threads of a Ti bolt before fastening. Picture below of Ti bolts, washers and nuts used on my strut bar. Ti socket cap head bolts tend to have the head tapered to distinguish them from garden variety stainless or aluminium bolts.

Picture of blue anodized Ti flanged nuts used for my shock absorber top mounts. The one smaller nut is for my Cusco Master Cylinder Stopper. Sorry, the magazine and hot babe on the cover is not included.
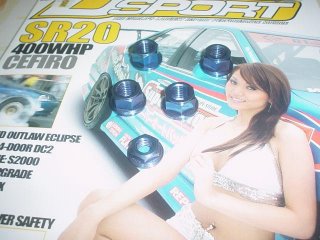
The Ti fasteners on my front carbon strut bar and front damper "pillow ball" top mounts
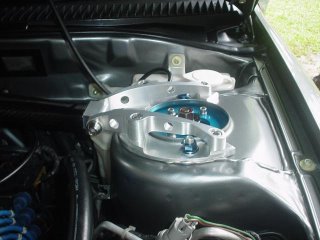
I guess I don't have to go into detail on stainless steel as most of you should be pretty familiar with this material. Oh and before I forget below are some of the suppliers of aerospace fasteners for motorsport or fast road application. Happy fastening!
AWF Pro-Bolt (UK)Supplies Prodrive WRC team.
Hyper Bolt (UK)
Poggipolini SPA (Italy). Supplies Ferrari F1 and Ducati WSB teams amongst others.
Mettec (US)
Redmist Motorsports (US)
SDC Tanaka (Japan)